There is a requirement for all building managers to ensure the safety of the public and employees so far as reasonably practicable. This requirement is set out in the Health and Safety at Work Act 1974, The Management of Health and Safety Regulations 1999, Control of Substances Hazardous to Health 2002, the HSE’s ACoP L8: “Legionnaires’ disease, the control of legionella bacteria in water systems”, the associated HSG274 Technical Guidance Part 2: “The control of legionella bacteria in hot and cold water systems” 2014 and the Department of Health’s HTM 04-01 “Safe Water in Healthcare Premises” Parts A, B and C, 2016.
What are Dead Legs and Blind Ends? 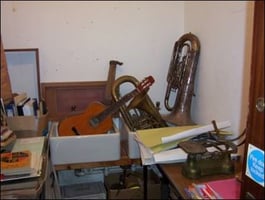
The Health Technical Memorandum 04-01 Part B defines a dead leg as a length of pipework leading to a fitting through which water only passes infrequently when there is a draw-off from a fitting, creating potential stagnation. HTM 04-01 Part A Section 12.5 sets out guidance that pipework length should not be greater than 3 metres from the ring main and no more than 2m from the TMV to the outlet. An example of this could be a water cooler which requires the water supply to come from a distance further than 3 metres and is in an area where few people use it.
A blind end is defined in HSG274 Part 2 as a length of pipework that is closed at one end through which no water passes. For example, where a wash hand basin in a room has been removed, so that the room can be used as a store or as an office, the basin supply pipework may be capped off leaving lengths of pipework containing stagnant water and creating blind ends on the hot and cold water services.
Both blind ends and dead legs increase the risk of biofilm forming and creating the right conditions for Legionella, Pseudomonas aeruginosa, and other waterborne pathogens to proliferate; thereby increasing the health risk to anyone using the water system.
Biofilm is defined as a community of bacteria and other microorganisms enclosed in a protective layer with entrained debris attached to a surface. The surfaces of pipework, water tanks, water outlets, shower heads and hoses are a few examples where biofilm can form.
How can they be managed?
Where water is allowed to stagnate, there is a risk of contamination. The key elements of managing the pipework distribution system are to keep the system clean, the water flowing, keep the hot water hot and cold water cold. In addition, the following points should also be considered;
- Ensure the Legionella risk assessment, schematic drawings, and as-fitted drawings are up to date and reviewed.
- In existing buildings where the use of a room containing a water outlet is changed requiring no water outlet, a reporting system must be in place to alert the relevant department e.g. estates department to ensure all pipework to the outlet is removed, ensuring that any “T”s are removed, back to the distribution loop. In Healthcare facilities the Water Safety Group (WSG) should monitor this regularly.
- I
f the outlet is to be retained and is low use, then an appropriate Legionella flushing regime should be put in place. HSG 274 Part 2, table 2.1 sets out guidance on the management of little-used outlets with a weekly flushing regime or as indicated by the Legionella risk assessment. It is important to note once a flushing regime has been implemented it is sustained and accurate water safety records of flushing are maintained.
- Where new buildings, extensions, or refurbishments are planned there is a risk the new building, extension, or refurbished area may be left empty between the time the contractors have moved out and the users of the building have moved in. During this period the area could become one large dead end. It is important to have a robust flushing regime and microbiological sampling regime in place until the building is returned to normal occupancy and use. Typically, the FM service provider or Estates team are the incumbent interim party who would be responsible to ensure that the flushing regime is carried out.
- Where new builds or extensions are planned it is important to involve the Water Safety Group and the estate's operational teams at the earliest stage of design to ensure the proposed water distribution system and any associated primary heating sources are going to be fit for purpose including the minimisation of the risk of dead legs and blind ends.
In design there needs to be certainty that on completion of the pipework, the water outlets particularly stand-alone water coolers, dishwashers, washing machines and specialised equipment requiring a water supply are going to be fitted and used. If there is doubt regarding the equipment, consideration should be given to leaving the water service supply out of the main contract and if required, installing the water supply post-contract.
- It is essential the water commissioning records for any new building, extension or refurbished are comprehensive and show the flow rates and temperature profiles for all outlets, water storage tanks and hot water generators. As fitted drawings, water system schematics, flushing records for when the building was unoccupied, commissioning data (including disinfection certificates) and Legionella risk assessments must all available at the building handover from the main contractor.
If you have questions regarding the issues raised above or you would like to speak with one of our consultants please click here to get in touch.
Editors Note: The information provided in this blog is correct at the date of original publication - June 2019 (Revised November 2023).
Image by (El Caminante) from Pixabay
© Water Hygiene Centre 2023